CONTACT US
- 13961432521(Manager Wang)
- 13813676349(Manager Zhu)
- zhuyun@czshcd.com
- Group 9, Caoqiao Village, Xueyan Town, Wujin District, Changzhou City
What should I pay attention to for zinc alloy bearing seats?
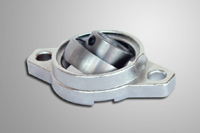
1. Control of alloy composition begins with the purchase of alloy ingots, which must be based on ultra-high purity zinc and made with ultra-high purity aluminum, magnesium, and copper. The supplier has strict composition standards. Excellent zinc based alloy materials are the guarantee for producing excellent castings.
"When purchasing alloy ingots, it is necessary to ensure that there is a clean and dry stacking area to avoid white rust caused by prolonged exposure to moisture, or increased slag generation and metal loss due to contamination by factory dirt.". A clean factory environment is important for effective control of alloy composition.
3. The ratio of new material to water inlet and other return materials shall not exceed 50%. Generally, new material: old material=70:30. In continuous remelting alloys, aluminum and magnesium gradually decrease.
When remelting the nozzle material, it is necessary to strictly control the remelting temperature not to exceed 430 ℃ to avoid loss of aluminum and magnesium.
5. Conditional zinc alloy bearing seat factories use a centralized melting furnace to melt zinc based alloys, making the alloy ingot and the return material evenly proportioned. The flux can be used more effectively to maintain uniform and stable alloy composition and temperature. Electroplating waste and fines should be separately melted in a furnace.