General points of machining design in Changzhou
Classification:Company NewsPublished:2023-03-09
[Content Overview] The introduction of Changzhou mechanical processing factory is to first analyze the workpiece with r···
The introduction of Changzhou mechanical processing factory is to first analyze the workpiece with reference to the part drawings, initially draw up a design plan for the inspection tool, determine the reference plane, concavity and convexity of the inspection tool, detect the cross section, positioning surface, and simply draw its two-dimensional schematic diagram. In the design of inspection tools, the specific design modeling of the inspection tool is the key, which directly affects whether the inspection tool can accurately detect the quality of the workpiece. Due to the characteristic of the body panels mainly featuring free form surfaces,“ Object Reverse” Is currently a common method for modeling. In order to achieve the inspection of the workpiece free surface by the inspection tool, it is generally necessary to maintain a constant gap of 3 or 5mm between the specific surface to be inspected and the inner surface of the workpiece. CNC machining machines can meet the requirements of high accuracy according to the designed surface numerical simulation. In actual inspection, the deviation of the workpiece surface can be measured by reciprocating movement of the inspection tool surface with a dedicated measuring tool. There are two main methods for detecting the outer contour of a workpiece. When designing the corresponding inspection tool, ① the specific surface extends outward by about 20mm along the tangential direction of the outer contour of the workpiece; ② Extend downward for about 20mm along the normal direction of the outer contour of the workpiece. Next, extend the curved surface along the tangent or normal direction of its contour for 20mm to obtain a specific inspection surface, and then extend it to the reference plane for a certain interval to inspect the specific model. Due to the complexity of vehicle body panels, the combination of the above two methods is mostly required when inspecting specific surfaces. However, for some special profiles, this is still difficult to achieve. 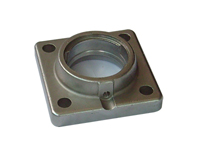
The detection of the critical surface of the workpiece is generally achieved through a section template. The section template of the inspection tool is divided into two types: rotary type and inserted type. When the span of the section template exceeds 300mm, it is usually designed as an inserted type to ensure the detection accuracy in the vertical direction. The specific surface detection is the inner surface of the workpiece, while the section template spans the outer surface of the workpiece to detect the outer surface of key sections. Generally, its working surface is 2-3 mm apart from the outer surface of the workpiece, and its modeling method is similar to that of the inspection tool surface. The plate material of the section template is generally a metal such as steel or aluminum, and the working surface can be made of aluminum or resin. Section templates with complex surfaces may interfere during rotation or insertion, and can be segmented in practical design
Stretch the specific upper surface along the reference plane direction for a certain interval to ensure that its extreme points are greater than 150mm thick to ensure sufficient strength for the inspection. At the same time, try to ensure that the specific bottom surface, i.e. the upper surface (base surface) of the floor assembly, is located in the integer position of the vehicle coordinate system. The inspection specific base plate assembly is generally composed of a base plate, channel steel (if necessary, processed in the middle), positioning blocks, and universal wheels. After the base plate is fixed by the inspection specific, other components can be selected as standard models based on actual conditions. Many important holes and flanges in vehicle body stamping parts need to be detected separately. In the design of inspection tools, a projection with a thickness of about 1mm is usually added to the upper surface of the inspection tool. The center of the projection is on the same axis as the center of the workpiece hole, and the diameter is 5mm larger than the aperture. Double lines are used for inspection on the projection. When the accuracy requirements of the measured hole are relatively high, the method of locating the hole is used to detect with a plug gauge and bushing.